The Vinyl Pool Liner
A structurally independent waterproofing alternative
A vinyl liner is a flexible, removable PVC pocket, placed on the pool's inner surface.
This means that, unlike traditional plaster, a vinyl liner is designed to be a separate waterproof layer
that is not permanently fixed to the pool's inner surface.
This aspect allows the liner to maintain its waterproofing in case of alterations to the underlying structure and facilitates its replacement if necessary.
The Drawbacks of the Structural Independence of Vinyl Liners
This structural independence also involves certain constraints:
The vinyl liner can deform, especially in foot traffic areas where bathers walk or step.
Insufficient adhesion between the liner and the pool's structure
(or the separation layer) on sloped areas can also promote the appearance of wrinkles or creases.
Moreover, the requirements in terms of conformity of the surface on which the liner will be
installed are particularly strict:
It is essential that the inner surface be flawless, without any imperfections such as sharp edges or roughness,
to prevent damaging the fragile vinyl liner.
The challenge of replicating the perfect fit of an original vinyl liner
Since the original vinyl liner is usually custom-fitted by the pool’s manufacturer,
it conforms perfectly to the pool when installed. However, when time comes to replace the liner,
creating a new one that matches the exact fit of the original becomes
challenging due to the precise measurements required:
When replacing an old vinyl liner, the new one must be made based on precise measurements of the structure:
A precision of ±0.5 cm for dimensions less than or equal to 1 meter and ±1 cm for dimensions greater than 1 meter.
In addition, the pool's angles must be clearly defined.
Errors are therefore possible not only during the taking of these measurements but also during
their interpretation prior to the liner's fabrication.
The Liner in Pool Renovations
It is often in the context of renovating old pools that the technical limitations of the vinyl liner become apparent. Apart from problems related to possible dimensional errors, its installation must be preceded by crucial preparation steps and compliance measures that are more or less constraining and costly.
The Alternative to Vinyl Liners
To avoid the constraints of traditionnal pool liners, some owners consider a structurally dependent finish as an alternative: plaster. However, this option presents notable disadvantages related to its structural dependence.
- Susceptibility to Support Cracks: Plaster, applied directly to the pool surface, is vulnerable to cracks and alterations of the surface on which it has been applied. Ground movements or thermal variations affecting the concrete structure can lead to cracks in the plaster, thus compromising the pool's waterproofing.
- Lack of Flexibility: Unlike liners, plaster does not adapt well to minor changes in the pool's structure. This rigidity increases the risk of long-term waterproofing and adhesion problems.
- Maintenance and Repair Difficulties: Repairing plaster is often more complex and costly than repairing a liner. It generally involves a complete draining and specialized masonry work.
- Aesthetic Limitations: Although plaster offers different finishes, it is less versatile than liners in terms of patterns, textures, and colors, thus limiting aesthetic options.
In summary, while plaster is attractive for its traditional aspect, it is essential to consider its structural limitations, particularly its dependence on the surface on which it has been applied and susceptibility to damage, which can impact the pool's durability and maintenance.
Why Replace a Liner with Resin?
The laminated, fiberglass-reinforced resin pool coating uniquely combines the benefits of structurally dependent finishes,
such as traditional plaster, with the flexibility of independent liners,
without their technical limitations.
Because the resin is applied in liquid form,
it eliminates the need for complex measurements, ensuring a perfect fit
that conforms seamlessly to the pool’s shape without wrinkles or creases.
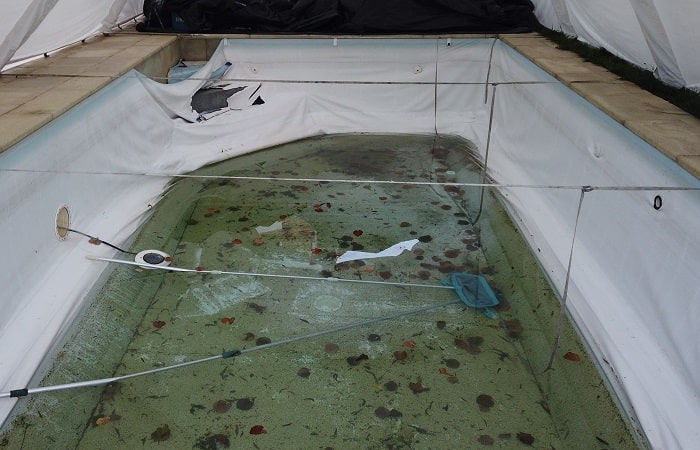
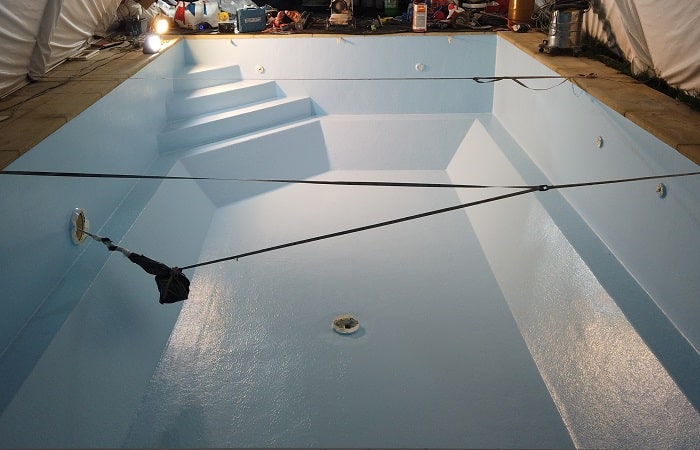
Like traditional plaster, reinforced resin has the ability to perfectly follow the contours and shapes of the pool, creating a smooth and homogeneous surface without wrinkles or precarious joints. However, unlike plaster, which is structurally dependent on the pool's inner surface to which it is applied, reinforced resin maintains a certain independence. This characteristic is crucial because it allows the coating to remain unaffected by potential micro-cracks in the pool's inner surface. Traditional plaster, being directly bonded to the pool's inner surface, is at risk of deteriorating and cracking if the inner surface degrades.
Reinforced Resin: Ideal for Renovating Old Pools
The reinforced resin coating is an ideal waterproofing solution for renovating old pools with inner surfaces that need reinforcement:
Before implementation, any cracks and damages are filled with a special thermosetting paste composed of resin and fibers.
This paste effectively seals imperfections and strengthens weakened areas, preparing the pool's inner surface for the lamination process.
Its implementation then involves the application of successive layers of reinforcement in the form of fiberglass mats (with a density varying between 300-450g/m²) and thermosetting liquid resin.
During this phase, called "lamination," any roughness of the pool's inner surface is entirely covered by the 3,5 - 4 millimeter thick composite lining.
This aspect of lamination makes it a particularly interesting solution for renovating pools whose surface roughness could damage a more flexible and delicate coating, like a liner.
The reinforced resin coating can, for example, be applied to old mosaic pools whose sharp-edged tiles tend to detach over time.
No Complex Measurements Required
The fabrication of a liner by the manufacturer is based on a plan of the pool, requiring precision of ±0.5 cm for dimensions less than or equal to 1 meter, and ±1 cm for larger dimensions. Errors can occur during the measurement process or the liner's manufacturing. A liner made with imprecise dimensions will not fit the pool correctly. The reinforced resin coating eliminates the risk of sizing errors. Applied directly on-site, it conforms seamlessly to the pool’s shapes and contours, ensuring perfect alignment with the structure.
Optimal Pool Enhancement
Reinforced resin provides freedom from the constraints posed by complex pool designs. The composite coating, along with its gelcoat finish, effortlessly conforms to the pool's contours, without wrinkles, seams, or structural weaknesses. It accentuates the pool's unique architecture, often obscured by poorly fitting liners.
High Mechanical Resistance
Compared to flexible liners, this 3.5 mm thick composite coating delivers exceptional resistance to punctures, tears, and abrasions, as well as wear from bathers' activities. In short, the fiberglass-reinforced resin coating seamlessly combines optimal waterproofing, durability, and aesthetics.
Wrinkles and Creases on Liners
One of the main drawbacks of liners is the presence of wrinkles and creases. The presence of wrinkles on a liner can be attributed to various causes, including:
— Inappropriate water treatment:
Creases can form due to poor management of chemical water treatments, such as insufficient pH or excessively high concentrations of disinfectants or their residues.
Excessive acidity of the water can contribute to the appearance of wrinkles and creases on the liner by affecting the mineral components contained in this coating.
— Presence of water under the liner:
A pool liner is a flexible, removable PVC pouch placed on the pool's structure.
Water that infiltrates through the pool's support can gradually accumulate between the liner and the structure.
While this water may eventually drain when the ground dries, moisture often persists.
Additionally, condensation can cause water to gather under the liner, as it is not fully
impermeable but rather offers a limited degree of water resistance.
In fact, liners "sweat" a few liters of water per day, averaging about 15 cl/m² per week.
Without proper drainage, water can accumulate beneath the membrane, creating stagnant pockets of water that foster microorganism growth, potentially leading to the slow deterioration of the liner.
Even the installation of antibacterial felt under the liner cannot fully eliminate this risk, as the felt itself can become saturated with stagnant water.
- Excessive water temperature:
Standard vinyl liners are typically designed to withstand water temperatures below 28°C.
Maintaining this temperature can be challenging during the summer, especially in pools covered by glazed shelters,
where the water tends to heat up quickly.
— Dimensional error:
A vinyl liner is prefabricated in a factory, relying on complex measurements.
The more intricate the pool's shape, the higher the risk of inaccuracies.
As a result, the liner may not perfectly fit the pool's surface, leading to wrinkles,
particularly in corners and around staircases.
— Insufficient adhesion between the liner and the support:
Poor adhesion can cause the liner to shift or slip, leading to wrinkles or creases,
particularly in high-traffic areas where bathers walk.
This issue can stem from various factors, such as the quality of the pool's surface,
the type of separating layer used, or flaws in the liner installation process.
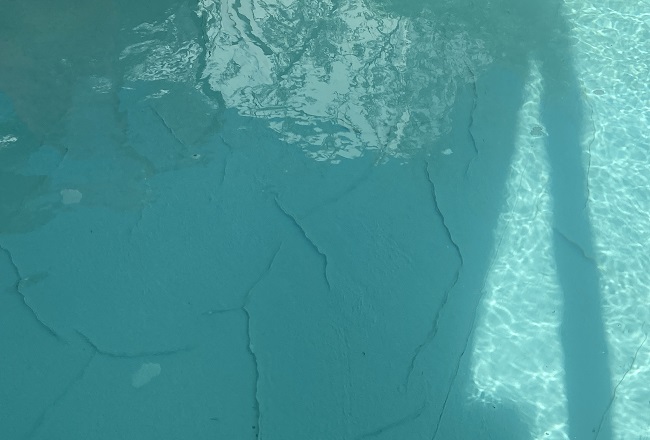
In short, impurities tend to accumulate between the wrinkles, turning them into breeding grounds for bacterial proliferation over time. This makes pool cleaning more difficult, increasing the risk of algae growth. Robotic cleaners may struggle to effectively reach certain areas, meaning walls often require manual cleaning to maintain the pool’s water quality.
Why is fiberglass-reinforced resin considered superior to liners?
Unlike vinyl liners, resin is applied in liquid form. When combined with fiberglass reinforcement, it creates a rigid, 3.5 mm thick, undeformable coating that hardens without wrinkles, seams, or weak joints.
It is a particularly sought-after waterproofing solution for its adaptability to complex shapes, allowing freedom from constraints imposed by complex pool configurations.
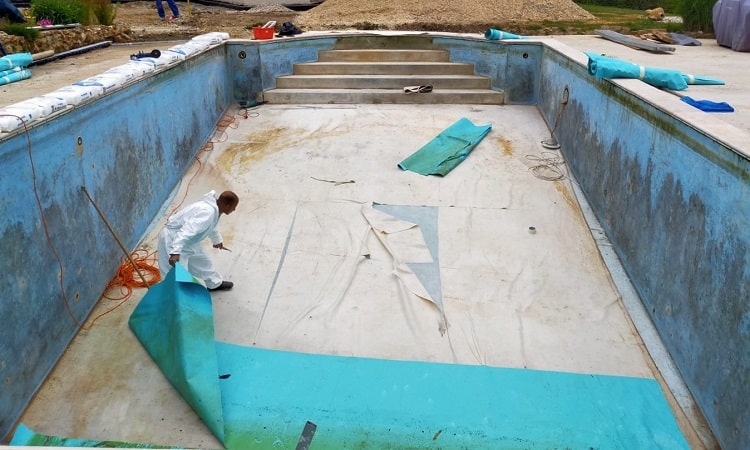
During the removal of a vinyl liner, the condition of the underlying pool structure becomes visible,
often revealing signs of humidity and mold.
In the case above, the vinyl liner will be replaced with a fiberglass-reinforced polyester resin coating.
This process starts with preparing the surface, followed by the application of a bonding primer.
The liquid resin is then applied directly to the pool’s surface, combined with fiberglass reinforcement.
As it hardens, the resin conforms perfectly to the pool’s contours, forming a rigid, fully waterproof layer that adheres seamlessly to the base, eliminating the risk of unsightly wrinkles.
Optimizing the Waterproofing of Fittings
Unlike vinyl liners, which require precise custom cuts for each fitting, reinforced resin seamlessly covers the junction between the pool’s surface and its fittings. It adheres tightly and uniformly around skimmers, return jets, and lights, ensuring no gaps or spaces through which water could infiltrate, providing enhanced and long-lasting waterproofing.
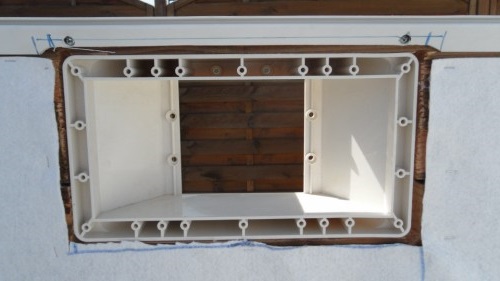
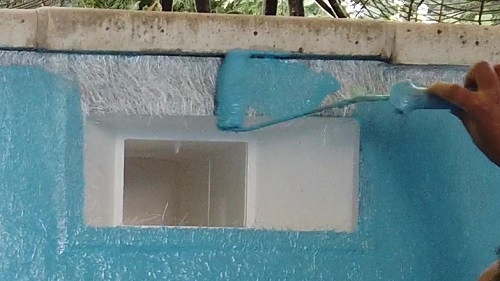
The Attachment method
The liner is typically attached to the pool edges using either a "Hung" or "Overlap" system. Over time, the exposed parts of the liner, especially in the corners, can become rigid, leading to shrinkage and eventual damage at the attachment points. This is caused by the slow, natural migration of plasticizers from the PVC-P material. Unlike PVC-P liners, polyester resin does not suffer from shrinkage. The resin coating is securely bonded to the lower part of the pool coping during installation, eliminating the need for a vulnerable fixation system prone to deterioration over time.
The Condition of the Pool's Structure
The condition of the concrete structure in older pools is often compromised due to ground movements, temperature fluctuations, and water infiltration following the loss of waterproofing from the old vinyl liner. Micro-cracks are frequently present.
Unlike fiberglass-reinforced polyester resin, which actively strengthens the pool structure, the liner is merely "placed" on the support without offering reinforcement.
It is not uncommon for small pieces of the aging support to detach behind the vinyl liner. These fragments, often sharp and abrasive, pose a significant risk of puncturing the flexible and vulnerable membrane.
The reinforced resin coating, applied as a thermosetting liquid, along with its bonding primer, penetrates the porous surface and
rough areas of the pool structure, providing the reinforcement and protection often required in pool renovations.
Advantages of Liners
- Inexpensive
- Easy to replace
Disadvantages of Liners
- Quick deterioration with water treatment errors
- Wrinkles, compromising hygiene
- Susceptible to perforations, tears, and cuts
- Deformation caused by foot traffic
- Moisture buildup under the liner, leading to rotting and loss of waterproofing
- Suboptimal for renovations
- Inability to remove certain stains
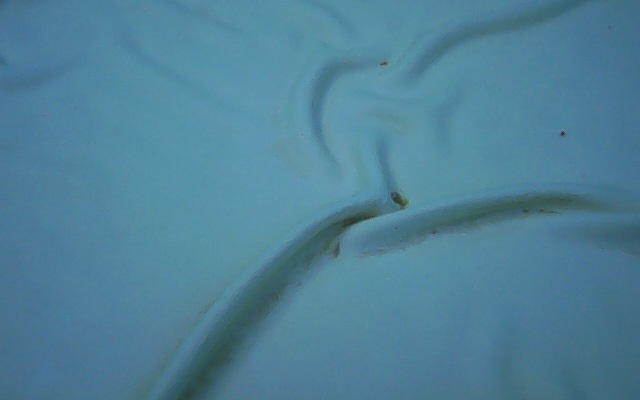
The Transformative Potential of Resin
Innovative and versatile, reinforced resin outperforms traditional liners with its unmatched ability to adapt seamlessly to any shape. Applied in liquid form, it hardens into a uniform, watertight coating that precisely follows even the most intricate configurations, enhancing the pool’s contours often hidden by ill-fitted liners. Perfect for renovations, it allows the seamless integration of new features, such as corner steps, while revitalizing the look of older pools. Its exceptional adaptability not only addresses structural imperfections but also ensures a tailored fit around fittings and fixtures, delivering durable and reliable waterproofing.
The Strength of Fiberglass Reinforced Polyester Resin
This 3.5 mm thick composite shell is engineered for superior durability and structural integrity.
By combining the flexibility of fiberglass with the toughness of polyester resin,
it forms a highly resistant barrier capable of withstanding the physical stresses of everyday use.
Unlike more fragile materials, this composite resists wear and tear over time,
maintaining its strength and resilience even under challenging conditions.
Its exceptional resistance to perforations and tears drastically reduces the risk of leaks,
providing long-lasting protection for the pool.
The Gelcoat
Once the laminated polyester resin and fiberglass have fully dried, the essential gelcoat finish is applied in two stages: a base layer of Gelcoat followed by a paraffin Topcoat to seal and complete the coating.
The Role of the Gelcoat Finish
The Gelcoat provides a smooth, seamless surface that is exceptionally easy to maintain.
Its uniform finish minimizes the buildup of impurities and greatly reduces the risk of algae growth.
This benefit is particularly evident after replacing a vinyl liner:
The perfectly smooth Gelcoat allows robotic cleaners to cover the entire pool surface
without any obstacles, such as creases or wrinkles, ensuring thorough cleaning.
This makes maintenance easier and reduces the need for cleaning products.
Repairs
In the event of damage from external factors, the gelcoat can be easily repaired. The process involves sanding the affected area and applying new layers of Resin, Fiberglass and Gelcoat. Once the repair is complete, the area will be fully waterproof and the damage will be virtually undetectable to the naked eye.
Advantages of Resin with Gelcoat
- Ideal for pools with complex designs and configurations
- No wrinkles, promoting better hygiene
- Easy-to-clean gelcoat finish
- Highly resistant to perforations, cuts, and tears
- Excellent durability against heavy foot traffic
- Minimizes buildup of impurities and algae
- Simple to repair in the event of external damage
- Perfect for pool renovations, offering long-lasting results
- Resistant to putrefaction
- Provides added protection for the underlying pool structure
Disadvantages of Resin with Gelcoat
- More expensive than vinyl liners
- Requires proper implementation by a qualified specialist
(Approximately one week of work + one week of drying for a 4 meters wide, 8 meter long pool)
Replacing a Pool Liner with Fiberglass Reinforced Resin

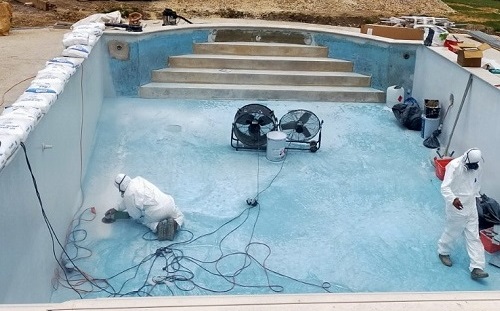
Once the liner is removed, several issues on the pool's support often become evident, including stains and mold. A thorough sanding process is essential to cleanse and prepare the surface for the next step: the manual application of the fiberglass-reinforced coating through lamination.
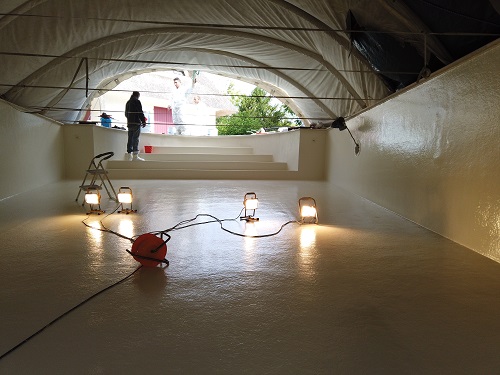
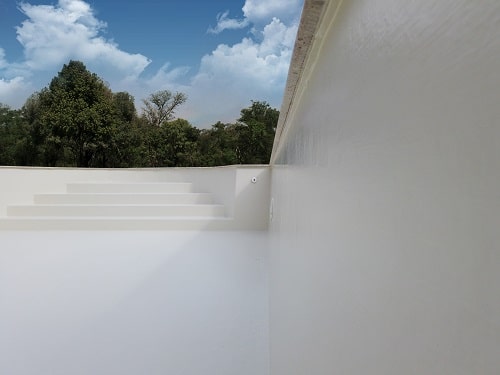
The reinforced resin creates a rigid, fully waterproof coating with a thickness of 3.5 mm. Unlike flexible vinyl liners, it eliminates issues related to the formation of wrinkles and creases, providing a smooth and durable finish.
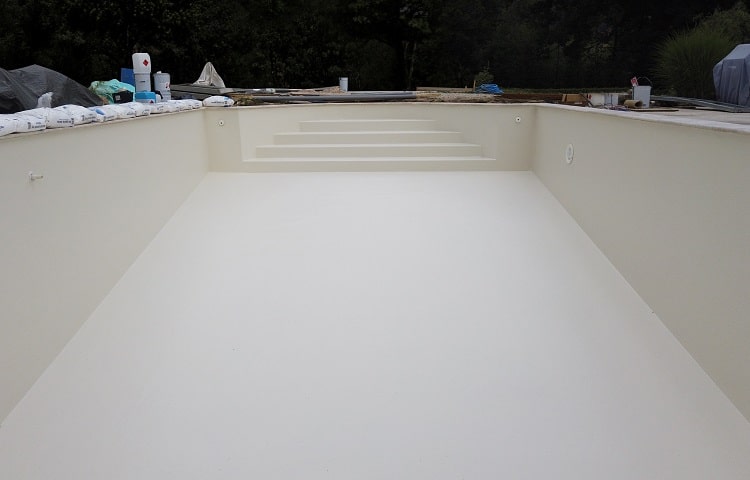
The light ivory Gelcoat finish (RAL 1015) enhances the pool’s aesthetics by subtly influencing the water’s color. A variety of shades are available, allowing owners to choose a finish that matches their desired style and ambiance.
Fiberglass Reinforced Resin Coating on a Complex-Shaped Diving Area
Below is an example of a pool with a complex-shaped diving area where the original vinyl liner
was poorly adapted to the pool's contours.
A fiberglass reinforced resin lining is always applied on-site, molding perfectly to the pool's exact shape.
This coating conforms precisely to the pool’s inner surface, ensuring an optimal fit and long-lasting waterproofing.
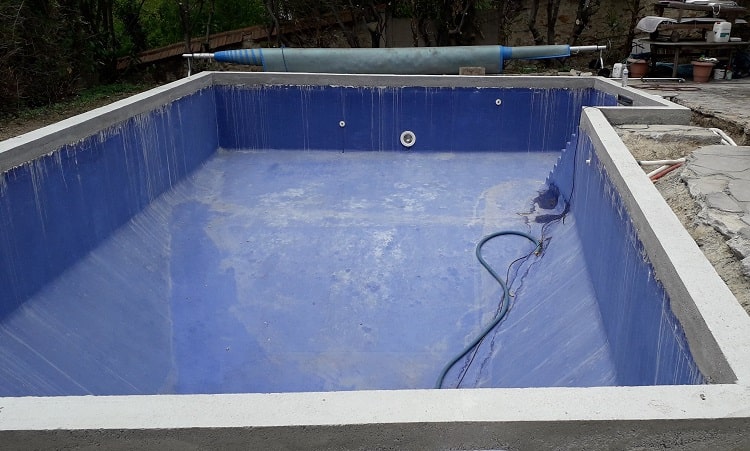
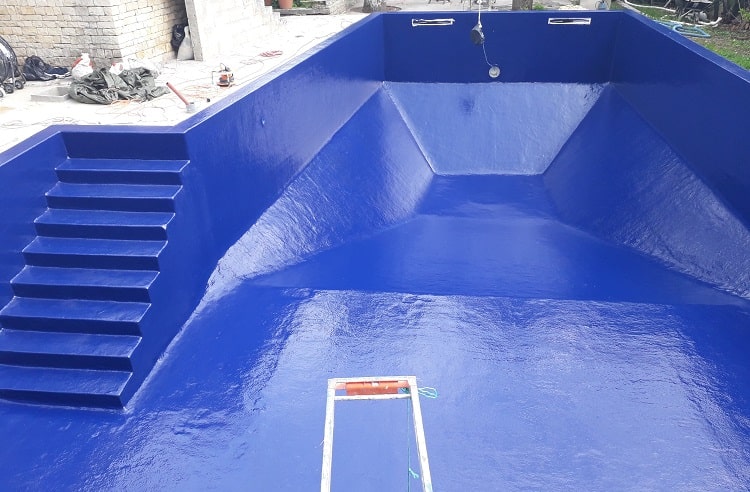
The rigid fiberglass-reinforced resin shell seamlessly conforms to the pool's contours, creating a continuous surface without wrinkles or weak seams. This effectively eliminates the risk of deformation caused by foot traffic, particularly around staircases and sloped areas.
Which Coating to Choose? Reinforced Resin or Vinyl Liner?
The choice ultimately depends on your budget, the pool's shape, and how much time you're willing to
dedicate to maintenance.
A vinyl pool liner is a renewable product, requiring periodic replacement, whereas a reinforced resin coating
is engineered for greater durability and long-lasting performance.
Fiberglass-reinforced polyester resin with a Gelcoat finish offers a more sophisticated solution,
blending functionality, longevity, and modern aesthetics.
This coating enhances your pool's appearance while eliminating many of the typical maintenance concerns.